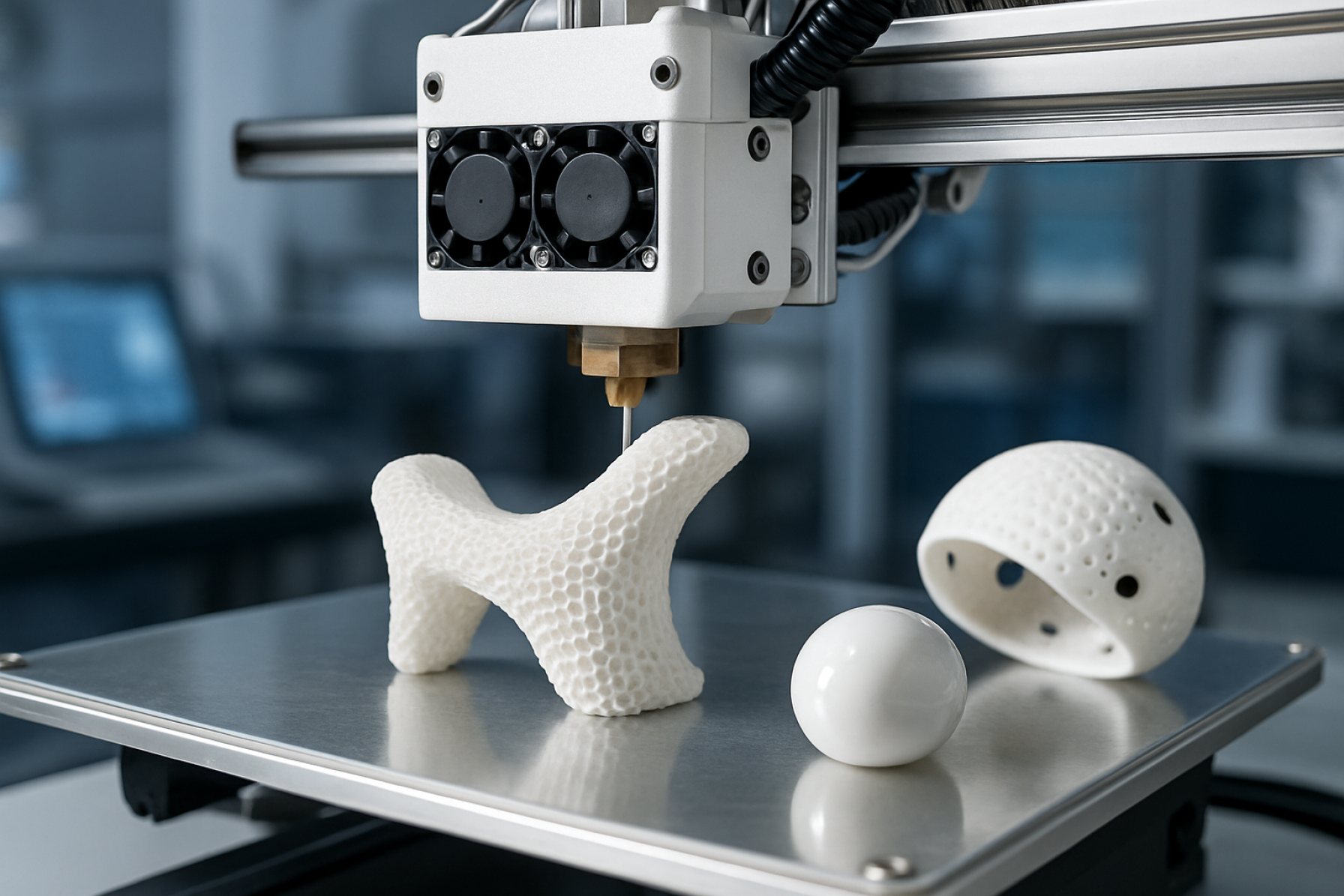
Revolutionierung medizinischer Implantate: Wie die extrusionbasierte additive Fertigung das Gesundheitswesen im Jahr 2025 und darüber hinaus prägt. Erforschen Sie das Marktwachstum, Durchbrüche und die nächste Innovationswelle.
- Zusammenfassung: Wichtige Trends und Markttreiber im Jahr 2025
- Marktgröße, Wachstumsrate und Prognose (2025–2030)
- Kerntechnologien: Fortschritte in der extrusionbasierten additive Fertigung
- Materialinnovationen: Biokompatible Polymere und Verbundwerkstoffe
- Regulatorische Landschaft und Standards für medizinische Implantate
- Führende Unternehmen und strategische Partnerschaften
- Klinische Anwendungen: Orthopädie, Zahnmedizin und darüber hinaus
- Fertigungsworkflow: Von der Planung zu patientenspezifischen Implantaten
- Herausforderungen: Qualitätssicherung, Skalierbarkeit und Kosten
- Zukünftige Aussichten: Neue Chancen und disruptive Trends
- Quellen & Referenzen
Zusammenfassung: Wichtige Trends und Markttreiber im Jahr 2025
Die extrusionbasierte additive Fertigung (AM), insbesondere die Fused Deposition Modeling (FDM) und das Direct Ink Writing (DIW), steht im Jahr 2025 und in den kommenden Jahren vor bedeutendem Wachstum im Bereich medizinischer Implantate. Die Fähigkeit dieser Technologie, patientenspezifische Implantate mit komplexen Geometrien, maßgeschneiderter Porosität und biokompatiblen Materialien zu fertigen, treibt die Akzeptanz in der Orthopädie, Zahnmedizin und kraniofazialen Anwendungen voran. Wichtige Trends und Markttreiber entstehen, während sich der Sektor weiter entwickelt und regulatorische Wege klarer werden.
Ein großer Trend im Jahr 2025 ist die zunehmende Verwendung von Hochleistungs-Thermoplasten wie Polyetheretherketon (PEEK) und Polyetherketonketon (PEKK) in der extrusionbasierten AM. Diese Materialien bieten mechanische Eigenschaften und Biokompatibilität, die mit traditionellen Implantatmetallen vergleichbar sind, während sie leichtere, röntgenstrahlendurchlässige und anpassbare Implantate ermöglichen. Unternehmen wie Stratasys und Evonik Industries entwickeln und liefern aktiv medizinische Filamente und Pulver und unterstützen den Übergang zu polymerbasierten Implantaten.
Ein weiterer wichtiger Treiber ist die Integration digitaler Workflows, von der Bildgebung und Planung bis hin zur Fertigung und Nachbearbeitung. Die Einführung fortschrittlicher Software und 3D-Scanning-Technologien ermöglicht eine schnelle, präzise Anpassung von Implantaten, reduziert die Produktionszeiten und verbessert die Patientenresultate. 3D Systems und Materialise sind bekannt für ihre End-to-End-Lösungen, die den Prozess von Patientendaten bis zum fertigen Implantat optimieren.
Regulatorischer Fortschritt formt ebenfalls den Markt. Im Jahr 2025 wird erwartet, dass mehr Extrusions-basierte AM-Implantate regulatorische Genehmigungen erhalten, insbesondere in den USA und der EU, da die Standards für additive Fertigung in medizinischen Geräten zunehmend etabliert werden. Dies ermutigt Krankenhäuser und Gerätehersteller, in interne 3D-Druckfähigkeiten zu investieren, wobei Unternehmen wie Stratasys und 3D Systems zertifizierte Hardware und validierte Workflows anbieten.
Mit Blick auf die Zukunft ist die Perspektive für die extrusionbasierte AM im Bereich medizinischer Implantate robust. Der Sektor wird voraussichtlich von fortlaufenden Materialinnovationen, zunehmender Automatisierung und der Ausweitung der Herstellung am Point of Care profitieren. Strategische Partnerschaften zwischen Materiallieferanten, Druckerherstellern und Gesundheitsdienstleistern werden wahrscheinlich die klinische Akzeptanz und Skalierung beschleunigen. Wenn die Technologie reift, wird die extrusionbasierte AM eine zentrale Rolle in der nächsten Generation personalisierter, hochleistungsfähiger medizinischer Implantate spielen.
Marktgröße, Wachstumsrate und Prognose (2025–2030)
Der Markt für extrusionbasierte additive Fertigung (AM) im Bereich medizinischer Implantate steht zwischen 2025 und 2030 vor robustem Wachstum, angetrieben von technologischen Fortschritten, regulatorischen Genehmigungen und zunehmender klinischer Akzeptanz. Die extrusionbasierte AM, insbesondere FDM und DIW, gewinnt an Bedeutung aufgrund ihrer Fähigkeit, patientenspezifische Implantate mit biokompatiblen Polymeren und Verbundwerkstoffen herzustellen.
Im Jahr 2025 wird der globale Markt für additive Fertigung im medizinischen Bereich auf mehrere Milliarden Dollar geschätzt, wobei extrusionbasierte Technologien einen bedeutenden und wachsenden Teil darstellen. Zu den Haupttreibern gehören die steigende Nachfrage nach personalisierter Gesundheitsversorgung, der Bedarf an schneller Prototypenerstellung und die Möglichkeit, komplexe Geometrien zu produzieren, die mit traditionellen Fertigungsmethoden nicht machbar sind. Die Einführung der extrusionbasierten AM ist insbesondere in der Orthopädie, der kranio-maxillofacialen und der zahnmedizinischen Implantatanwendung bemerkenswert.
Wichtige Akteure der Branche wie Stratasys und 3D Systems haben ihre medizinischen Portfolios erweitert und bieten extrusionbasierte Drucker sowie validierte medizinische Materialien an. Stratasys hat eine steigende Nachfrage nach seinen FDM-Lösungen in der chirurgischen Planung und der Implantat-Prototypenentwicklung gemeldet, während 3D Systems weiterhin mit Gesundheitsdienstleistern zusammenarbeitet, um regulatorisch konforme Workflows für patientenspezifische Geräte zu entwickeln. Darüber hinaus liefert Evonik Industries Hochleistungs-Polymere wie PEEK und bioresorbierbare Materialien, die für die extrusionbasierte AM geeignet sind und damit das Marktwachstum unterstützen.
Von 2025 bis 2030 wird der Markt für extrusionbasierte AM für medizinische Implantate voraussichtlich eine jährliche Wachstumsrate (CAGR) im hohen einstelligen bis niedrigen zweistelligen Bereich erleben, was einige traditionelle Fertigungssegmente übertrifft. Dieses Wachstum wird durch fortlaufende klinische Studien, zunehmende FDA- und CE-Zulassungen für 3D-gedruckte Implantate sowie die Integration digitaler Workflows in Krankenhäusern und chirurgischen Zentren unterstützt. Die Region Asien-Pazifik, angeführt von China und Indien, wird voraussichtlich eine beschleunigte Akzeptanz aufgrund des ausgebauten Gesundheitsinfrastruktur und staatlichen Initiativen, die medizinische Innovation unterstützen, sehen.
Mit Blick auf die Zukunft bleibt die Marktperspektive positiv, da sich die Technologien der extrusionbasierten AM weiter entwickeln. In den nächsten Jahren werden voraussichtlich weitere Materialinnovationen, verbesserte Druckerzuverlässigkeit und eine breitere Akzeptanz von 3D-gedruckten Implantaten in der regulären klinischen Praxis zu erwarten sein. Strategische Partnerschaften zwischen Druckerherstellern, Materiallieferanten und Gesundheitseinrichtungen werden entscheidend für die Skalierung der Produktion und die Erfüllung regulatorischer Anforderungen sein. Daher wird die extrusionbasierte additive Fertigung bis 2030 zunehmend integraler Bestandteil der Lieferkette für medizinische Implantate.
Kerntechnologien: Fortschritte in der extrusionbasierten additive Fertigung
Die extrusionbasierte additive Fertigung (AM), insbesondere FDM und DIW, hat sich als Kerntechnologie zur Herstellung medizinischer Implantate schnell weiterentwickelt. Im Jahr 2025 verzeichnet der Sektor bedeutende Fortschritte in den Materialwissenschaften, der Prozesskontrolle und der regulatorischen Akzeptanz, die die Produktion patientenspezifischer Implantate mit verbesserten mechanischen und biologischen Leistungen ermöglichen.
Ein wesentlicher Treiber der jüngsten Innovation ist die Entwicklung von medizinischen Thermoplasten und Verbundfilamenten, die für extrusionbasierte Prozesse maßgeschneidert sind. Unternehmen wie Stratasys und 3D Systems haben ihre Portfolios erweitert, um biokompatible Polymere wie PEEK, Polycaprolacton (PCL) und Polymilchsäure (PLA) einzuschließen, die für tragende und resorbierbare Implantate geeignet sind. Diese Materialien werden nun in kranio-fazialen, maxillofazialen und orthopädischen Anwendungen verwendet, wobei laufende klinische Studien ihre Wirksamkeit unterstützen.
Die Prozessautomatisierung und Echtzeitüberwachung transformieren ebenfalls die extrusionbasierte AM. Fortschrittliche Extrusionssysteme verfügen nun über geschlossene Rückkopplungen und in-situ-Qualitätskontrollen, die eine dimensionale Genauigkeit und Wiederholbarkeit sicherstellen – entscheidend für die regulatorische Konformität in der Herstellung medizinischer Geräte. Ultimaker (jetzt Teil von UltiMaker) und Renishaw haben Sensorarrays und KI-gesteuerte Prozessanalysen in ihre Plattformen integriert, die eine konsistente Produktion komplexer Geometrien und Gitterstrukturen ermöglichen, die die Osseointegration und Implantatstabilität verbessern.
Ein weiterer bemerkenswerter Trend ist die Einführung der Multimaterial-Extrusion, die die Herstellung von Implantaten mit abgestuften Eigenschaften oder eingebetteten Arzneimittelabgabefunktionen ermöglicht. Dieser Ansatz wird von Forschungsabteilungen innerhalb von Evonik Industries, einem führenden Anbieter von Hochleistungs-Polymeren, sowie von Herstellern medizinischer Geräte untersucht, die mit Anbietern von AM-Technologien zusammenarbeiten, um nächste Generation bioaktive Implantate zu entwickeln.
Die regulatorischen Wege entwickeln sich parallel zu den technologischen Fortschritten. Die U.S. Food and Drug Administration (FDA) und die Europäische Arzneimittelagentur (EMA) haben aktualisierte Leitlinien für 3D-gedruckte medizinische Geräte herausgegeben, die den Genehmigungsprozess für extrusionsbasierte Implantate, die robuste Qualitätssicherung und Rückverfolgbarkeit aufweisen, rationalisieren. Diese regulatorische Klarheit wird voraussichtlich den Markteintritt neuer Produkte in den nächsten Jahren beschleunigen.
Mit Blick auf die Zukunft ist die extrusionbasierte AM bereit, den Sektor der medizinischen Implantate weiter zu beeinflussen. Die Konvergenz fortschrittlicher Biomaterialien, digitalem Design und automatisierter Fertigung ermöglicht die Produktion von vollständig maßgeschneiderten, patientenspezifischen Implantaten in großen Stückzahlen. Branchenführer wie Stratasys, 3D Systems und Evonik Industries werden voraussichtlich weitere Innovationen vorantreiben, mit einem Fokus auf die Ausweitung klinischer Indikationen und die Verbesserung der Patientenresultate durch personalisierte Medizin.
Materialinnovationen: Biokompatible Polymere und Verbundwerkstoffe
Im Jahr 2025 verzeichnet die extrusionbasierte additive Fertigung (AM) für medizinische Implantate bedeutende Fortschritte in den Materialwissenschaften, insbesondere in der Entwicklung und dem Einsatz von biokompatiblen Polymeren und Verbundwerkstoffen. Der Fokus liegt auf Materialien, die nicht nur strengen regulatorischen Anforderungen in Bezug auf Sicherheit und Wirksamkeit entsprechen, sondern auch verbesserte mechanische Eigenschaften, Bioaktivität und Verarbeitbarkeit bieten, die auf patientenspezifische Implantate zugeschnitten sind.
Polymilchsäure (PLA), Polycaprolacton (PCL) und Polyetheretherketon (PEEK) bleiben grundlegende Polymere in der extrusionbasierten AM für medizinische Anwendungen. Insbesondere PEEK gewinnt aufgrund seiner hohen Festigkeit, chemischen Beständigkeit und Röntgendurchlässigkeit an Bedeutung, was es für tragende orthopädische und spinalen Implantate geeignet macht. Unternehmen wie Victrex und Evonik Industries stehen an der Spitze der Bereitstellung von medizinischem PEEK und verwandten Hochleistungs-Polymeren, mit laufenden Investitionen zur Erweiterung ihrer Portfolios, um der wachsenden Nachfrage nach maßgeschneiderten Implantatlösungen gerecht zu werden.
In den letzten Jahren gab es einen Anstieg in der Entwicklung von Verbundfilamenten, bei denen Polymere mit bioaktiven Keramiken (z.B. Hydroxylapatit, Trikalziumphosphat) oder Kohlefaser verstärkt werden, um die Osteointegration und die mechanischen Eigenschaften zu verbessern. Stratasys und 3D Systems arbeiten aktiv mit Gesundheitsdienstleistern und Forschungseinrichtungen zusammen, um solche Verbundwerkstoffe für klinische Anwendungen zu validieren und zu kommerzialisieren. Diese Verbundwerkstoffe sind besonders vielversprechend für kraniofaziale, zahnmedizinische und orthopädische Implantate, bei denen maßgeschneiderte mechanische Eigenschaften und Bioaktivität entscheidend sind.
Ein weiterer bemerkenswerter Trend ist die Integration von antimikrobiellen Wirkstoffen und arzneimittelabgebenden Funktionen in extrusionbasierte Filamente. Dieser Ansatz soll postchirurgische Infektionen reduzieren und die lokale Heilung fördern. Unternehmen wie SABIC erforschen Polymermischungen und Additive, die über extrusionbasierte AM verarbeitet werden können und dabei Biokompatibilität und regulatorische Konformität aufrechterhalten.
Mit Blick auf die Zukunft wird erwartet, dass die nächsten Jahre weitere Innovationen in smarten und reaktiven Materialien bringen, wie z.B. Formgedächtnis-Polymere und stimuli-responsive Verbundwerkstoffe, die sich an physiologische Bedingungen anpassen oder therapeutische Wirkstoffe nach Bedarf freisetzen können. Die fortlaufende Zusammenarbeit zwischen Materiallieferanten, Herstellern medizinischer Geräte und Regulierungsbehörden wird voraussichtlich die klinische Übersetzung dieser fortschrittlichen Materialien beschleunigen. Während die Systeme der extrusionbasierten AM immer ausgeklügelter werden, mit verbesserter Temperaturkontrolle und Multimaterialfähigkeiten, wird die Palette an biokompatiblen Polymeren und Verbundwerkstoffen, die für medizinische Implantate geeignet sind, weiterhin erweitert, was den Trend zu personalisierten und funktionalisierten Implantatlösungen unterstützt.
Regulatorische Landschaft und Standards für medizinische Implantate
Die regulatorische Landschaft für die extrusionbasierte additive Fertigung (AM) von medizinischen Implantaten entwickelt sich schnell weiter, da sich die Technologie reift und die Akzeptanz in klinischen Umgebungen beschleunigt. Im Jahr 2025 intensivieren Regulierungsbehörden und Normungsorganisationen ihre Anstrengungen, um die Sicherheit, Wirksamkeit und Qualität von 3D-gedruckten medizinischen Implantaten sicherzustellen, mit einem besonderen Fokus auf extrusionbasierte Techniken wie FDM und DIW.
Die U.S. Food and Drug Administration (FDA) bleibt an der Spitze, nachdem sie Leitdokumente veröffentlicht hat, die sich spezifisch mit den technischen Überlegungen für additive gefertigte medizinische Geräte befassen. Das Zentrum für Geräte und strahlenmedizinische Gesundheit (CDRH) der FDA aktualisiert kontinuierlich seine Empfehlungen und betont die Validierung von Prozessen, die Materialcharakterisierung und die Nachbearbeitungskontrollen für die extrusionbasierte AM. Im Jahr 2024 und 2025 wird die FDA voraussichtlich weitere Anforderungen für patientenspezifische Implantate klären, einschließlich der Vorabgenehmigungen und Qualitätssystemregulierungen, die auf die einzigartigen Risiken der schichtweisen Herstellung zugeschnitten sind.
In Europa arbeiten die Europäische Arzneimittelagentur (EMA) und das Europäische Komitee für Normung (CEN) zusammen, um die Standards im Rahmen der Medical Device Regulation (MDR 2017/745) zu harmonisieren. Die MDR, die seit 2021 vollständig in Kraft ist, deckt nun explizit 3D-gedruckte Implantate ab, und laufende Aktualisierungen im Jahr 2025 werden voraussichtlich Rückverfolgbarkeit, Reproduzierbarkeit und Biokompatibilität für die extrusionbasierte AM ansprechen. Die Internationale Organisation für Normung (ISO) und ASTM International entwickeln ebenfalls aktiv Standards und überarbeiten diese, wie z.B. ISO/ASTM 52900 und ISO 17296, die Terminologie, Prozesskontrollen und Testprotokolle für AM in medizinischen Anwendungen bereitstellen.
Branchenführer, darunter Stratasys und 3D Systems, arbeiten eng mit Regulierungsbehörden und Normungsorgane zusammen, um sicherzustellen, dass ihre auf Extrusion basierenden Plattformen den sich entwickelnden Anforderungen entsprechen. Diese Unternehmen investieren in Qualitätsmanagementsysteme und Rückverfolgbarkeit, und nehmen an Pilotprogrammen teil, um regulatorische Einreichungen für maßgeschneiderte Implantate zu rationalisieren. Beispielsweise hat Stratasys sein Portfolio an medizinischen Materialien erweitert und arbeitet mit Krankenhäusern zusammen, um Workflows unter realen regulatorischen Bedingungen zu validieren.
Mit Blick auf die Zukunft wird erwartet, dass die regulatorische Perspektive für die extrusionbasierte AM im Bereich medizinischer Implantate robuster und global harmonisiert wird. Wichtige Trends umfassen die Integration digitaler Dokumentationsstränge, einen erhöhten Fokus auf die Überwachung während des Prozesses und die Einführung risikobasierter Ansätze sowohl für Materialien als auch für fertige Geräte. Während die regulatorische Klarheit zunimmt, wird der Weg für die klinische Akzeptanz von 3D-gedruckten Implantaten auf Basis der Extrusion voraussichtlich beschleunigt und die Innovation gefördert, während die Sicherheit der Patienten gewahrt bleibt.
Führende Unternehmen und strategische Partnerschaften
Da die extrusionbasierte additive Fertigung (AM) weiterhin an Bedeutung im Sektor der medizinischen Implantate gewinnt, gestalten mehrere führende Unternehmen und strategische Partnerschaften die Landschaft im Jahr 2025. Diese Technologie, zu der FDM und die direkte Extrusion biokompatibler Materialien gehören, wird genutzt, um patientenspezifische Implantate, chirurgische Führungen und Gerüste für die Gewebeengineering herzustellen.
Zu den bekanntesten Akteuren gehört Stratasys, das weiterhin ein globaler Marktführer in der extrusionbasierten AM ist, mit einer speziellen Gesundheitsabteilung, die sich auf medizinische Modelle und maßgeschneiderte Implantate konzentriert. Die FDM-Technologie des Unternehmens wird häufig zur Herstellung anatomischer Modelle und chirurgischer Planungstools verwendet und hat sein Portfolio um biokompatible Thermoplasten für temporäre und permanente Implantate erweitert. Im Jahr 2024 und 2025 hat Stratasys Kooperationen mit großen Krankenhausnetzwerken und Herstellern medizinischer Geräte angekündigt, um die Akzeptanz von 3D-gedruckten Implantaten zu beschleunigen.
Ein weiterer wichtiger Akteur, 3D Systems, hat seine Position durch seine auf Extrusion basierenden Lösungen und Partnerschaften mit Gesundheitsdienstleistern gestärkt. Der Fokus des Unternehmens auf regulatorische Compliance und Materialinnovation hat es ihm ermöglicht, patientenspezifische kraniale und maxillofaziale Implantate zu liefern. Im Jahr 2025 erweitert 3D Systems seine strategischen Allianzen mit akademischen medizinischen Zentren zur gemeinsamen Entwicklung neuer implantierbarer Geräte und zur Rationalisierung der klinischen Übersetzung von AM-Technologien.
In Europa ist Evonik Industries ein wichtiger Anbieter von Hochleistungs-Polymeren wie Polyetheretherketon (PEEK) und Polyamid 12 (PA12), die häufig in der extrusionbasierten AM für medizinische Anwendungen verwendet werden. Die Partnerschaften von Evonik mit Druckerherstellern und Herstellern medizinischer Geräte haben zur Kommerzialisierung neuer Sorten von implantierbaren Materialien geführt, wobei laufende Forschungen zu bioresorbierbaren Polymeren für nächste Generation Implantate stattfinden.
Strategische Partnerschaften treiben ebenfalls Innovationen voran. Zum Beispiel hat Ultimaker (jetzt Teil von UltiMaker nach der Fusion mit MakerBot) Kooperationen mit Krankenhäusern und Forschungsinstituten geschlossen, um offene Extrusionsplattformen für den medizinischen Einsatz zu entwickeln. Diese Initiativen zielen darauf ab, den Zugang zu maßgeschneiderter Implantatfertigung zu demokratisieren, insbesondere in ressourcenarmen Umgebungen.
Mit Blick auf die Zukunft wird in den nächsten Jahren voraussichtlich eine weitere Konsolidierung und sektorübergreifende Partnerschaften stattfinden, während die regulatorischen Wege für Extrusion-basierte AM-Implantate klarer werden und die Materialportfolios erweitert werden. Unternehmen konzentrieren sich zunehmend auf End-to-End-Lösungen, die Design, Fertigung und Nachbearbeitung integrieren, um strengen medizinischen Standards gerecht zu werden. Die fortgesetzte Beteiligung etablierter Branchenführer und das Auftreten neuer Akteure zeigen eine robuste Perspektive für die extrusionbasierte additive Fertigung im Sektor der medizinischen Implantate bis 2025 und darüber hinaus.
Klinische Anwendungen: Orthopädie, Zahnmedizin und darüber hinaus
Die extrusionbasierte additive Fertigung (AM), insbesondere FDM und DIW, schreitet in klinischen Anwendungen in der Orthopädie, Zahnmedizin und anderen Bereichen der medizinischen Implantate im Jahr 2025 rapide voran. Diese Technologie ermöglicht die Herstellung patientenspezifischer Implantate mit komplexen Geometrien, maßgeschneiderter Porosität und kontrollierten mechanischen Eigenschaften, die für eine erfolgreiche Integration und Funktion im menschlichen Körper entscheidend sind.
In der Orthopädie wird die extrusionbasierte AM verwendet, um kundenspezifische Knochengerüste und Gelenkimplantate herzustellen. Unternehmen wie Stratasys und 3D Systems stehen an der Spitze und bieten medizinische Drucker und biokompatible Materialien an, die für tragende Anwendungen geeignet sind. Beispielsweise wird die FDM-Technologie von Stratasys genutzt, um anatomische Modelle und chirurgische Leitfäden zu erstellen, während laufende Forschungen und Pilotprojekte den Einsatz für permanente Implantate, insbesondere für kraniofaziale und spinale Rekonstruktionen, erweitern. Die Fähigkeit, mit Hochleistungs-Polymeren wie PEEK (Polyetheretherketon) und medizinischem PLA zu drucken, erweitert die klinischen Indikationen.
Im dentalen Sektor revolutioniert die extrusionbasierte AM die Produktion von Kronen, Brücken und kieferorthopädischen Geräten. Envista Holdings und Dentsply Sirona nutzen extrusionbasierte Systeme, um schnelle, direkt verwendbare Lösungen für Zahnmediziner zu liefern. Diese Systeme ermöglichen die direkte Herstellung temporärer und permanenter Restaurationen, was die Durchlaufzeiten verkürzt und die Patientenresultate verbessert. Die Integration digitaler Workflows, von intraoralen Scans bis hin zu 3D-Druck, wird voraussichtlich in den nächsten Jahren zum Standard in Zahnarztpraxen werden.
Über die Orthopädie und Zahnmedizin hinaus wird die extrusionbasierte AM für Anwendungen wie patientenspezifische Atemwegsstents, Schädelplatten und sogar bioresorbierbare Implantate für pädiatrische Patienten erforscht. Evonik Industries, ein wichtiger Anbieter von medizinischen Polymeren, arbeitet mit Herstellern von Geräten zusammen, um neue druckbare Biomaterialien zu entwickeln, die die Geweberegeneration und die kontrollierte Abgabe von Medikamenten unterstützen. Der Einsatz der extrusionbasierten AM zur Herstellung poröser Implantate, die das Knochenwachstum fördern, ist ein wichtiger Bereich der klinischen Forschung, mit laufenden klinischen Studien in Europa und Nordamerika.
Mit Blick auf die Zukunft wird erwartet, dass sich die regulatorischen Wege klarer definieren, während die Implantate auf Basis der Extrusion von Pilotstudien in den regulären klinischen Gebrauch übergehen. Die U.S. Food and Drug Administration (FDA) und die Europäische Arzneimittelagentur (EMA) engagieren sich aktiv mit Industrievertretern, um Standards für Sicherheit, Wirksamkeit und Rückverfolgbarkeit zu etablieren. Während sich die Materialportfolios erweitern und die Druckfähigkeiten verbessern, wird die extrusionbasierte AM bereit sein, eine zentrale Rolle in der nächsten Generation personalisierter medizinischer Implantate zu spielen, mit signifikantem Wachstum, das bis 2025 und darüber hinaus zu erwarten ist.
Fertigungsworkflow: Von der Planung zu patientenspezifischen Implantaten
Die extrusionbasierte additive Fertigung (AM), insbesondere FDM und DIW, wird zunehmend zentral im Workflow zur Herstellung patientenspezifischer medizinischer Implantate im Jahr 2025. Der Prozess beginnt mit fortschrittlicher Bildgebung – typischerweise CT oder MRT – um die Anatomie des Patienten zu erfassen. Diese Daten werden mithilfe spezialisierter medizinischer Software in 3D-Modelle umgewandelt, die eine präzise Anpassung der Implantatgeometrie ermöglichen. Der digitale Workflow gewährleistet, dass Implantate an die individuellen anatomischen Anforderungen angepasst werden, was Passform und klinische Ergebnisse verbessert.
Sobald das Design abgeschlossen ist, wird das Modell in Maschinenanweisungen für extrusionbasierte 3D-Drucker übersetzt. Im medizinischen Sektor werden häufig biokompatible Thermoplaste wie Polyetheretherketon (PEEK), Polymilchsäure (PLA) und Polycaprolacton (PCL) sowie Verbundfilamente, die Keramiken oder bioaktive Wirkstoffe enthalten, verwendet. Unternehmen wie Stratasys und 3D Systems haben extrusionbasierte Plattformen entwickelt, die in der Lage sind, medizinische Materialien zu verarbeiten, mit regulatorischen Genehmigungen für bestimmte Anwendungen. Evonik Industries ist ein wichtiger Anbieter von Hochleistungs-Polymeren, einschließlich medizinischem PEEK, und unterstützt die Materialversorgungskette für diese Workflows.
Der Extrusionsprozess selbst ist hoch automatisiert und zunehmend in Qualitätssicherungssysteme integriert. Die Überwachung der Extrusionsparameter, der Schichthaftung und der dimensionalen Genauigkeit in Echtzeit wird zum Standard, was den Bedarf an Nachbearbeitung reduziert und die Wiederholbarkeit sichert. Zum Beispiel hat Apium Additive Technologies auf medizinische PEEK-Extrusion spezialisiert und bietet Drucker mit in-situ Prozessüberwachung und Rückverfolgbarkeitsfunktionen an, die auf regulierte Umgebungen zugeschnitten sind.
Nach dem Drucken durchlaufen Implantate Nachbearbeitungsschritte wie Sterilisation, Oberflächenveredelung und, wo erforderlich, die Addition bioaktiver Beschichtungen zur Verbesserung der Osseointegration. Der gesamte Workflow unterliegt strengen Validierungs- und Dokumentationsanforderungen, um den Vorschriften für medizinische Geräte, wie sie von der FDA oder der europäischen MDR durchgesetzt werden, zu entsprechen. Unternehmen wie LimaCorporate und Materialise sind bemerkenswert für ihre End-to-End-Lösungen, von der Planung bis zu fertigen, patientenspezifischen Implantaten, die die extrusionbasierte AM sowohl für Prototypen- als auch für die endgültige Teilproduktion nutzen.
Mit Blick auf die Zukunft wird in den nächsten Jahren erwartet, dass die Integration von KI-gesteuerter Designoptimierung, erweiterten Materialportfolios (einschließlich bioresorbierbarer und Arzneimittelausgabefilamente) und eine größere Automatisierung in der Nachbearbeitung voranschreiten. Die Konvergenz von digitalen Gesundheitsakten, Bildgebung und AM steht bereit, den Workflow zu optimieren, Durchlaufzeiten zu verkürzen und die On-Demand-Produktion von Implantaten am Point of Care zu ermöglichen. Während sich die regulatorischen Rahmenbedingungen anpassen, wird die extrusionbasierte AM bereit sein, eine zentrale Rolle im Bereich der personalisierten Medizin zu spielen.
Herausforderungen: Qualitätssicherung, Skalierbarkeit und Kosten
Die extrusionbasierte additive Fertigung (AM), insbesondere FDM und DIW, wird zunehmend als Option für die Produktion von medizinischen Implantaten erforscht. Doch während sich der Sektor 2025 weiterentwickelt, bestehen mehrere Herausforderungen bezüglich Qualitätssicherung, Skalierbarkeit und Kosteneffizienz.
Die Qualitätssicherung bleibt ein zentrales Anliegen. Medizinische Implantate erfordern strenge mechanische Eigenschaften, Biokompatibilität und dimensionale Genauigkeit. Variabilität in den Ausgangsmaterialien, wie z.B. medizinischen Polymeren und Verbundwerkstoffen, kann zu Inkonsistenzen in den gedruckten Teilen führen. Unternehmen wie Stratasys und 3D Systems, beide große Akteure im Bereich des medizinischen 3D-Drucks, haben proprietäre Materialformulierungen und Prozesskontrollen entwickelt, um diese Probleme zu beheben, doch branchenweite Standards entwickeln sich weiterhin. Das Fehlen allgemein akzeptierter Protokolle für die Überwachung während des Prozesses und die Validierung der Nachbearbeitung kompliziert die regulatorische Genehmigung, insbesondere für patientenspezifische Implantate. Organisationen wie ASTM International arbeiten an der Standardisierung, doch die breite Akzeptanz ist noch im Gange.
Die Skalierbarkeit stellt ein weiteres erhebliches Hindernis dar. Während die extrusionbasierte AM hervorragend darin ist, benutzerdefinierte, niedrigvolumige Implantate herzustellen, ist es herausfordernd, die Produktion zu skalieren, um die breitere klinische Nachfrage zu decken. Der schichtweise Charakter des Extrusionsprozesses beschränkt die Produktionsgeschwindigkeit. Unternehmen wie Evonik und Ensinger, die Hochleistungs-Polymere für medizinische Anwendungen liefern, investieren in Materialinnovationen, um schnellere Abscheidegeschwindigkeiten und verbesserte Druckbarkeit zu ermöglichen. Die Integration von Automatisierung und Multikopf-Drucksystemen, wie sie in aktuellen Entwicklungen von Stratasys zu sehen sind, befindet sich jedoch noch in den frühen Phasen für medizinische Anwendungen. Darüber hinaus erhöht der Bedarf an rigoroser Nachbearbeitung (z.B. Sterilisation, Oberflächenveredelung) die Komplexität der Skalierungsoperationen.
Die Kosten bleiben ein Hindernis für die weitverbreitete Akzeptanz. Die Preise für medizinische Polymere, wie z.B. PEEK und PEKK, sind aufgrund strenger Reinheits- und Rückverfolgbarkeitsanforderungen hoch. Darüber hinaus sind die Investitionen in validierte Systeme für die extrusionbasierte AM, Reinraumeinrichtungen und Infrastruktur zur Qualitätskontrolle erheblich. Während Unternehmen wie 3D Systems und Stratasys daran arbeiten, die Systemkosten zu senken und den Durchsatz zu verbessern, ist das wirtschaftliche Argument für die extrusionbasierte AM derzeit am stärksten für komplexe, patientenspezifische Implantate, bei denen die traditionelle Fertigung weniger praktikabel ist.
Mit Blick auf die Zukunft werden in den nächsten Jahren voraussichtlich schrittweise Verbesserungen erfolgen. Die fortlaufende Zusammenarbeit zwischen Materiallieferanten, Geräteherstellern und Regulierungsbehörden wird wahrscheinlich zu besseren Prozesskontrollen, robustereren Standards und schrittweisen Kostensenkungen führen. Dennoch wird die Überwindung der miteinander verbundenen Herausforderungen von Qualität, Skalierbarkeit und Kosten entscheidend für die breitere Akzeptanz von ekstrusionsbasierter AM für medizinische Implantate bis 2025 und darüber hinaus bleiben.
Zukünftige Aussichten: Neue Chancen und disruptive Trends
Da die extrusionbasierte additive Fertigung (AM) weiterhin reift, ist ihre Rolle im Sektor der medizinischen Implantate auf dem Weg zu einer bedeutenden Expansion bis 2025 und den folgenden Jahren. Die Fähigkeit dieser Technologie, patientenspezifische Implantate mit komplexen Geometrien, maßgeschneiderter Porosität und bioaktiven Materialien herzustellen, treibt sowohl die klinische Akzeptanz als auch die industrielle Investition voran. Mehrere wichtige Trends und Chancen gestalten die zukünftige Landschaft.
Einer der prominentesten Trends ist die Integration fortschrittlicher Biomaterialien in die Prozesse der extrusionbasierten AM. Unternehmen konzentrieren sich zunehmend auf biokompatible Polymere wie Polyetheretherketon (PEEK), Polymilchsäure (PLA) und Polycaprolacton (PCL), sowie Verbundfilamente, die Keramiken oder bioaktive Wirkstoffe enthalten. Beispielsweise entwickeln Stratasys und 3D Systems aktiv extrusionbasierte Lösungen für medizinische Polymere, die die Herstellung von Implantaten ermöglichen, die die mechanischen und biologischen Eigenschaften von native Geweben besser nachahmen können.
Die regulatorische Akzeptanz schreitet ebenfalls voran, da extrusionsbasierte AM-Implantate zunehmend Genehmigungen auf den wichtigsten Märkten erhalten. Die U.S. Food and Drug Administration (FDA) hat Leitlinien für 3D-gedruckte medizinische Geräte herausgegeben, und mehrere extrusion-gedruckte Implantate sind bereits klinisch in Gebrauch. Diese regulatorische Dynamik wird voraussichtlich beschleunigen, insbesondere da mehr Hersteller robuste Qualitätskontrollen und Rückverfolgbarkeit in ihren extrusionbasierten Workflows nachweisen.
Automatisierung und die Integration digitaler Workflows werden die traditionelle Implantatfertigung stören. Unternehmen wie Materialise sind Pioniere vollständiger digitaler Plattformen, die den Design- bis Produktionsprozess rationalisieren, die Durchlaufzeiten verkürzen und maßgeschneiderte Lösungen ermöglichen. Die Konvergenz der extrusionbasierten AM mit künstlicher Intelligenz und fortschrittlicher Bildgebung wird voraussichtlich die Präzision und Personalisierung medizinischer Implantate weiter verbessern.
Mit Blick auf die Zukunft wird der Markt voraussichtlich einen Anstieg der Herstellung am Point of Care erleben, wo Krankenhäuser und Kliniken extrusionbasierte AM-Systeme vor Ort einsetzen, um Implantate für einzelne Patienten herzustellen. Dieser Trend wird durch die Entwicklung kompakter, benutzerfreundlicher Extrusionsdrucker und validierter medizinischer Materialien unterstützt. Stratasys und 3D Systems gehören zu den Unternehmen, die Partnerschaften mit Gesundheitsdienstleistern erkunden, um solche dezentralen Fertigungsmodelle zu ermöglichen.
Zusammenfassend wird die extrusionbasierte additive Fertigung kurz davor sein, den Sektor der medizinischen Implantate durch Materialinnovationen, regulatorischen Fortschritt, digitale Integration und dezentrale Produktion zu transformieren. Wenn sich diese Trends zusammenführen, wird in den nächsten Jahren mit einer breiteren klinischen Akzeptanz, neuen therapeutischen Anwendungen und einer Neudefinition der Art und Weise, wie medizinische Implantate entworfen, produziert und ausgeliefert werden, gerechnet.
Quellen & Referenzen
- Stratasys
- Evonik Industries
- 3D Systems
- Materialise
- Ultimaker
- Renishaw
- Victrex
- Europäische Arzneimittelagentur (EMA)
- Europäisches Komitee für Normung (CEN)
- Internationale Organisation für Normung (ISO)
- ASTM International
- Envista Holdings
- Dentsply Sirona
- Apium Additive Technologies
- LimaCorporate
- Ensinger