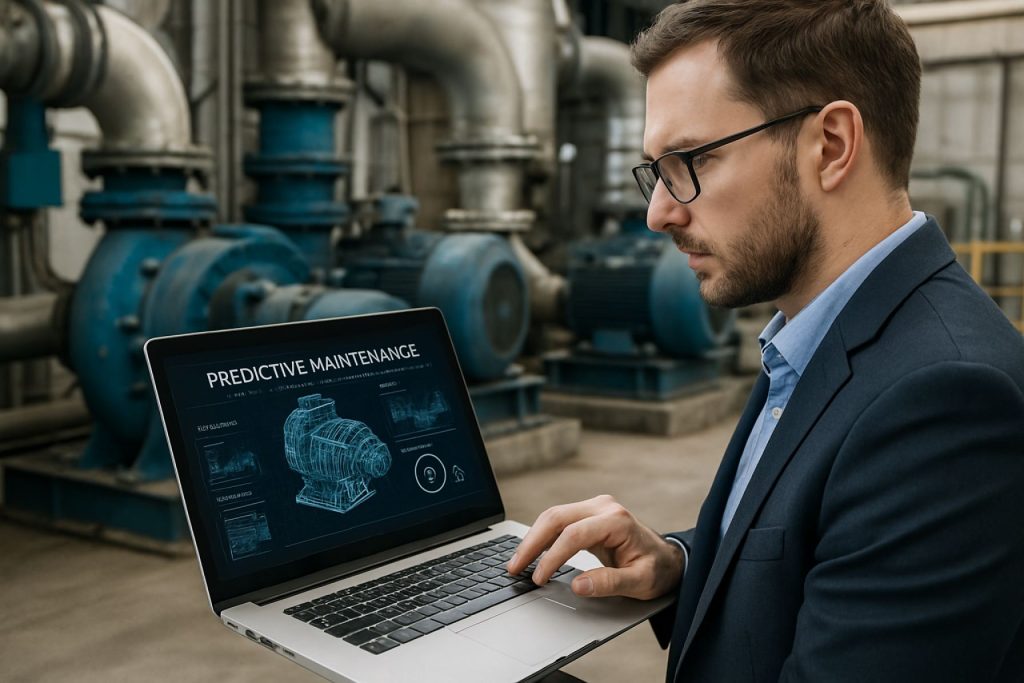
2025 Predictive Maintenance for Industrial Digital Twins Market Report: Unveiling AI-Enabled Efficiency, Market Dynamics, and Strategic Opportunities. Explore Key Trends, Forecasts, and Competitive Insights Shaping the Next 5 Years.
- Executive Summary & Market Overview
- Key Technology Trends in Predictive Maintenance for Digital Twins
- Competitive Landscape and Leading Players
- Market Growth Forecasts and Revenue Projections (2025–2030)
- Regional Analysis: Adoption and Investment Hotspots
- Challenges, Risks, and Emerging Opportunities
- Future Outlook: Strategic Recommendations and Innovation Pathways
- Sources & References
Executive Summary & Market Overview
Predictive maintenance for industrial digital twins is rapidly transforming asset management and operational efficiency across manufacturing, energy, and process industries. Digital twins—virtual replicas of physical assets, systems, or processes—enable real-time monitoring and simulation, while predictive maintenance leverages advanced analytics and machine learning to anticipate equipment failures before they occur. The convergence of these technologies is driving a paradigm shift from reactive and scheduled maintenance to data-driven, condition-based strategies.
In 2025, the global market for predictive maintenance solutions integrated with industrial digital twins is projected to reach new heights, fueled by the proliferation of Industrial Internet of Things (IIoT) devices, increased adoption of cloud computing, and the growing need to minimize unplanned downtime. According to Gartner, digital twin technology revenue is expected to surpass $20 billion by 2025, with a significant portion attributed to predictive maintenance applications.
- Market Drivers: Key drivers include the rising cost of equipment failure, stringent regulatory requirements for safety and reliability, and the competitive imperative to optimize asset utilization. The integration of AI-powered analytics with digital twins enables early detection of anomalies, reducing maintenance costs by up to 30% and extending asset lifespans, as reported by McKinsey & Company.
- Industry Adoption: Sectors such as oil & gas, automotive, aerospace, and utilities are at the forefront, leveraging predictive maintenance to enhance operational resilience. For example, Siemens and GE Digital have deployed digital twin platforms that integrate predictive analytics for turbine, pump, and motor maintenance.
- Regional Trends: North America and Europe lead in adoption due to advanced industrial infrastructure and high digital maturity, while Asia-Pacific is experiencing rapid growth driven by manufacturing expansion and government initiatives supporting Industry 4.0, as highlighted by IDC.
Looking ahead to 2025, the predictive maintenance for industrial digital twins market is poised for robust growth, underpinned by technological advancements, increasing digitalization, and a clear return on investment for early adopters. As organizations seek to future-proof their operations, the integration of predictive maintenance with digital twins will become a cornerstone of smart manufacturing and asset management strategies.
Key Technology Trends in Predictive Maintenance for Digital Twins
Predictive maintenance for industrial digital twins is rapidly evolving, driven by advances in artificial intelligence (AI), machine learning (ML), edge computing, and the integration of Internet of Things (IoT) sensors. In 2025, several key technology trends are shaping the landscape, enabling more accurate, real-time, and cost-effective maintenance strategies for industrial assets.
- AI-Driven Anomaly Detection: The adoption of advanced AI and ML algorithms is enhancing the ability of digital twins to detect anomalies and predict equipment failures with greater precision. These models leverage vast datasets from operational sensors, historical maintenance records, and contextual data to identify subtle patterns that precede faults. Companies like Siemens and GE Digital are at the forefront, integrating AI-powered analytics into their digital twin platforms to deliver actionable insights and reduce unplanned downtime.
- Edge Computing Integration: The shift toward edge computing allows predictive maintenance algorithms to run closer to the source of data—on-site at factories or within industrial equipment. This reduces latency, enables faster decision-making, and minimizes the need for constant cloud connectivity. According to Gartner, by 2025, over 50% of industrial digital twin deployments will incorporate edge analytics to support real-time maintenance interventions.
- IoT Sensor Proliferation and Interoperability: The increasing deployment of advanced IoT sensors—measuring vibration, temperature, pressure, and more—provides richer, high-frequency data streams for digital twins. Enhanced interoperability standards, such as OPC UA and MQTT, are facilitating seamless data integration across heterogeneous industrial environments, as highlighted by IDC.
- Cloud-Native Digital Twin Platforms: Cloud-native architectures are enabling scalable, flexible, and collaborative digital twin solutions. Providers like Microsoft Azure and AWS are offering platforms that support predictive maintenance workflows, from data ingestion to visualization and automated alerting.
- Integration with Enterprise Systems: Seamless integration with enterprise asset management (EAM), manufacturing execution systems (MES), and ERP platforms is becoming standard. This ensures that predictive maintenance insights from digital twins are directly actionable within existing business processes, as noted by Accenture.
These technology trends are collectively driving the adoption and effectiveness of predictive maintenance in industrial digital twins, resulting in improved asset reliability, reduced operational costs, and enhanced productivity across sectors such as manufacturing, energy, and transportation.
Competitive Landscape and Leading Players
The competitive landscape for predictive maintenance solutions within the industrial digital twins market is rapidly evolving as both established technology giants and specialized startups vie for market share. In 2025, the sector is characterized by strategic partnerships, acquisitions, and a focus on integrating artificial intelligence (AI) and machine learning (ML) to enhance predictive capabilities.
Leading players include IBM, GE Digital, Siemens, and PTC, all of which have robust digital twin platforms with embedded predictive maintenance modules. IBM’s Maximo Application Suite, for example, leverages AI-driven analytics to predict equipment failures and optimize maintenance schedules, while GE Digital’s Predix platform is widely adopted in heavy industries for its real-time asset performance management and predictive insights.
Emerging competitors such as AVEVA and Bentley Systems are gaining traction by offering industry-specific digital twin solutions with advanced predictive maintenance features, particularly in sectors like oil & gas, utilities, and manufacturing. These companies differentiate themselves through deep domain expertise and the ability to integrate with legacy industrial systems.
The market is also witnessing increased activity from cloud service providers such as Microsoft Azure and Google Cloud, which are leveraging their scalable infrastructure and AI toolkits to enable predictive maintenance at scale. Their platforms appeal to enterprises seeking flexible, cloud-native digital twin deployments.
- IBM and Siemens are frequently cited as market leaders due to their comprehensive portfolios and global reach, as noted in the Gartner Magic Quadrant for Industrial IoT Platforms.
- Startups such as Uptake and C3 AI are innovating with AI-first approaches, offering predictive maintenance solutions that promise faster deployment and lower total cost of ownership.
Overall, the competitive landscape in 2025 is marked by consolidation, ecosystem partnerships, and a race to deliver more accurate, real-time predictive maintenance insights through digital twins. The ability to integrate seamlessly with existing industrial assets and provide actionable, data-driven recommendations remains a key differentiator among leading players.
Market Growth Forecasts and Revenue Projections (2025–2030)
The market for predictive maintenance solutions within the industrial digital twins sector is poised for robust growth in 2025, driven by the increasing adoption of Industry 4.0 technologies and the need for operational efficiency across manufacturing, energy, and process industries. According to recent analyses, the global predictive maintenance market—of which digital twins are a rapidly expanding segment—is expected to reach a valuation of approximately $10.7 billion in 2025, up from $6.9 billion in 2022, reflecting a compound annual growth rate (CAGR) of over 15% MarketsandMarkets. Within this, the industrial digital twin submarket is anticipated to account for a significant share, as enterprises increasingly integrate real-time data analytics and machine learning into their digital twin platforms for predictive maintenance applications.
Revenue projections for predictive maintenance solutions leveraging digital twins are particularly strong in asset-intensive sectors such as oil & gas, automotive, and utilities. For instance, the manufacturing sector alone is projected to contribute over 30% of the total market revenue in 2025, as companies invest in digital twin-enabled predictive maintenance to minimize downtime and extend equipment lifecycles Gartner. The energy sector is also expected to see accelerated adoption, with digital twins being deployed for predictive maintenance of turbines, grids, and pipelines, leading to improved reliability and cost savings.
- Regional Outlook: North America is forecasted to maintain its lead in market share through 2025, driven by early technology adoption and significant investments from major industrial players. However, Asia-Pacific is expected to exhibit the fastest growth rate, fueled by rapid industrialization and government initiatives supporting smart manufacturing IDC.
- Technology Trends: The integration of AI and IoT with digital twins is anticipated to further accelerate market growth, enabling more accurate failure predictions and prescriptive maintenance actions.
- Vendor Landscape: Leading technology providers such as Siemens, IBM, and GE Digital are expected to expand their predictive maintenance offerings, driving both innovation and competition in the market.
Overall, 2025 is set to be a pivotal year for predictive maintenance in industrial digital twins, with strong revenue growth and expanding adoption across key verticals and regions.
Regional Analysis: Adoption and Investment Hotspots
The adoption and investment landscape for predictive maintenance in industrial digital twins is marked by significant regional disparities, driven by factors such as industrial maturity, digital infrastructure, government initiatives, and sectoral focus. As of 2025, North America and Western Europe remain the primary hotspots, with Asia-Pacific rapidly closing the gap due to aggressive digitalization and manufacturing modernization.
In North America, the United States leads in both adoption and investment, propelled by the presence of major industrial players, advanced IoT infrastructure, and a robust ecosystem of technology vendors. The region benefits from strong collaboration between industrial firms and technology providers, with sectors such as oil & gas, automotive, and aerospace at the forefront. According to IDC, U.S. manufacturing companies are expected to increase their spending on digital twin-enabled predictive maintenance solutions by over 18% year-over-year through 2025.
Western Europe, particularly Germany, the UK, and France, is another key region, driven by Industry 4.0 initiatives and government-backed digital transformation programs. The German government’s “Industrie 4.0” strategy has catalyzed widespread adoption of digital twins and predictive analytics in manufacturing and process industries. Statista projects that the European digital twin market will reach $8.4 billion by 2025, with predictive maintenance accounting for a significant share of this growth.
The Asia-Pacific region is emerging as a dynamic investment hotspot, led by China, Japan, and South Korea. China’s “Made in China 2025” policy and Japan’s Society 5.0 initiative are accelerating the integration of digital twins and predictive maintenance in manufacturing, energy, and transportation sectors. According to Mordor Intelligence, Asia-Pacific is expected to register the fastest CAGR in digital twin adoption through 2025, driven by large-scale smart factory deployments and government incentives.
- North America: Mature market, high investment, strong vendor ecosystem.
- Western Europe: Policy-driven adoption, focus on manufacturing and process industries.
- Asia-Pacific: Fastest growth, government-led digitalization, expanding industrial base.
Other regions, such as the Middle East and Latin America, are in earlier stages but show growing interest, particularly in oil & gas and mining. Overall, regional adoption and investment in predictive maintenance for industrial digital twins in 2025 are closely tied to digital maturity, sectoral priorities, and supportive policy frameworks.
Challenges, Risks, and Emerging Opportunities
Predictive maintenance for industrial digital twins is rapidly transforming asset management and operational efficiency, but the sector faces a complex landscape of challenges, risks, and emerging opportunities as it matures in 2025. One of the primary challenges is data integration. Industrial environments typically involve heterogeneous equipment and legacy systems, making it difficult to aggregate and harmonize data streams necessary for accurate predictive analytics. This fragmentation can lead to incomplete digital representations and suboptimal maintenance predictions, as highlighted by Gartner.
Cybersecurity risks are also intensifying. As digital twins become more interconnected with operational technology (OT) and information technology (IT) networks, the attack surface expands. Vulnerabilities in predictive maintenance platforms could expose critical infrastructure to cyber threats, potentially leading to operational disruptions or safety incidents. IBM Security notes a significant uptick in targeted attacks on industrial IoT and digital twin environments, underscoring the need for robust security protocols.
Another risk is the reliance on high-quality, real-time data. Predictive maintenance algorithms depend on accurate sensor inputs and historical data. Inconsistent data quality, sensor failures, or communication lags can degrade model performance, resulting in false positives or missed failure predictions. This can erode trust in digital twin solutions and hinder broader adoption, as reported by Accenture.
Despite these challenges, several emerging opportunities are shaping the market. The integration of artificial intelligence (AI) and machine learning (ML) with digital twins is enabling more sophisticated anomaly detection and failure prediction, reducing unplanned downtime and maintenance costs. McKinsey & Company estimates that advanced predictive maintenance could reduce maintenance costs by up to 30% and cut breakdowns by 70% in some industries.
Additionally, the rise of edge computing is addressing latency and bandwidth issues by processing data closer to the source, enabling faster and more reliable predictive insights. Partnerships between industrial firms and technology providers are accelerating innovation, with companies like Siemens and GE investing heavily in scalable, secure digital twin platforms.
In summary, while predictive maintenance for industrial digital twins faces significant integration, data quality, and security challenges, the convergence of AI, edge computing, and strategic partnerships is unlocking new value and operational resilience for industrial enterprises in 2025.
Future Outlook: Strategic Recommendations and Innovation Pathways
The future outlook for predictive maintenance within industrial digital twins is shaped by rapid technological advancements, evolving industry needs, and the increasing integration of artificial intelligence (AI) and machine learning (ML) into operational workflows. As we approach 2025, organizations are expected to move beyond pilot projects and scale predictive maintenance solutions across entire production lines and asset fleets, leveraging digital twins as the central data and simulation hub.
Strategically, companies should prioritize the following recommendations to maximize value:
- Invest in Interoperability and Open Standards: Seamless integration between digital twin platforms, IoT devices, and enterprise systems is critical. Adopting open standards such as OPC UA and supporting APIs will enable data sharing and analytics across heterogeneous environments, as highlighted by Gartner.
- Advance AI-Driven Analytics: The next wave of predictive maintenance will rely on self-learning algorithms capable of detecting subtle anomalies and predicting failures with higher accuracy. Companies like IBM and Siemens are investing in AI-powered digital twin solutions that continuously refine their models using real-time operational data.
- Focus on Edge Computing: Processing data at the edge—closer to the source—reduces latency and bandwidth costs, enabling faster anomaly detection and response. According to IDC, by 2025, over 50% of industrial data will be processed at the edge, making edge-enabled digital twins a strategic imperative.
- Enhance Cybersecurity: As digital twins become more interconnected, the attack surface expands. Implementing robust cybersecurity frameworks and continuous monitoring is essential to protect sensitive operational data, as emphasized by NIST.
- Promote Workforce Upskilling: The adoption of predictive maintenance and digital twins requires new skill sets in data science, AI, and systems integration. Leading manufacturers are partnering with educational institutions and technology providers to bridge the talent gap, as reported by World Economic Forum.
Innovation pathways for 2025 and beyond include the convergence of digital twins with augmented reality (AR) for immersive maintenance support, the use of blockchain for secure data provenance, and the development of industry-specific digital twin templates. As these technologies mature, predictive maintenance will shift from reactive and scheduled interventions to a truly proactive, autonomous paradigm, driving significant cost savings and operational resilience across industries.
Sources & References
- McKinsey & Company
- Siemens
- GE Digital
- IDC
- AWS
- Accenture
- IBM
- AVEVA
- Google Cloud
- Uptake
- C3 AI
- MarketsandMarkets
- Statista
- Mordor Intelligence
- NIST